Dissertation
Silk Denim
The Tango region in Northern Kyoto prefecture has a long history of being a production area of silk fabrics that spans approximately 1,300 years and it remains the largest producer in Japan even today. The area boasts a collection of weaving houses that produce traditional textiles such as the widely renowned Tango Chirimen. One of these irreplaceable workshops, "Sosaku Kobo Ito Asobi" continues to challenge themselves by trying to create their own unique fabrics that take advantage of techniques that have been cultivated since old times.
Category: | Material |
---|
Date: | 2025.01.07 |
---|
Tags: | #silkdenim #ss25 #visvim #wmv |
---|
The Tango region in Northern Kyoto prefecture has a long history of being a production area of silk fabrics that spans approximately 1,300 years and it remains the largest producer in Japan even today. The area boasts a collection of weaving houses that produce traditional textiles such as the widely renowned Tango Chirimen. One of these irreplaceable workshops, "Sosaku Kobo Ito Asobi" continues to challenge themselves by trying to create their own unique fabrics that take advantage of techniques that have been cultivated since old times. They possess a great variety of looms that can produce dobby weaves, jacquard weaves, and karami weaves (leno weaves) and can also handle everything from twisting, dyeing and weaving in house, which makes it possible for them to produce new textiles on a regular basis as it is possible for them to work with any given material and apply a range of diverse techniques that are at their disposal.
The jacquard woven fabric that consists of kenbo slub yarn and kenchuu yarn, which has been named "silk denim" at visvim was something that came into existence by utilizing the workshop's unique techniques. Kenbo slub yarn consists of threads that are extracted from the cocoon unsuitable for use as raw silk due to fibers that are short which then get twisted and spun into a yarn that deliberately preserves the natural knots that get created. Kenchuu yarn is a yarn that is spun from even shorter fibers that are produced as a byproduct of creating kenbo yarn. Both yarns are characterized by a light and soft texture having high heat retention, however because of their delicate nature where they tend to break if pulled too hard (when tension is applied) during weaving it is only possible to weave with an old shuttle loom that operates at a slower speed.
The "silk denim" material is a double weave (a technique where you weave multiple sets of warp and weft yarns that intertwine to create a two layer fabric) that utilizes both types of yarn to form the outer and inner facing sides. Each side is interchangeably woven in a way where one side has the kenchuu yarn visible on the surface and the reverse side has the kenbo slub yarn appear on that surface. The unique texture of the reverse side gave way to the name of this material that has been likened to a denim which develops greater character over time. It can be said that this fabric was born from a reversal of conventional thinking as it utilizes the fabric surface which is normally hidden by making the inner side the outer surface.
A shuttle loom is a loom in which a shuttle containing weft threads moves back and forth from side to side, and when the weft threads are folded over at both ends of the fabric the organization of yarns that is formed prevents fraying, known as the "mimi (ear)." This detail known in English as "selvedge" is an essential part within the world of vintage denim and can also be found on our silk denim.
"It is difficult to weave a soft silk thread on a loom. It's necessary to constantly monitor the thread when it's on the loom to see if it has broken. As it's also not possible to see the reverse side of the fabric I'm unable to take my eyes away while the process unfolds as I'm checking things the entire time the fabric is being woven," explains Toru Yamamoto, the second-generation owner of the workshop. This workshop openly accepts requests to take on unordinary work that can be difficult and helps make them a reality.

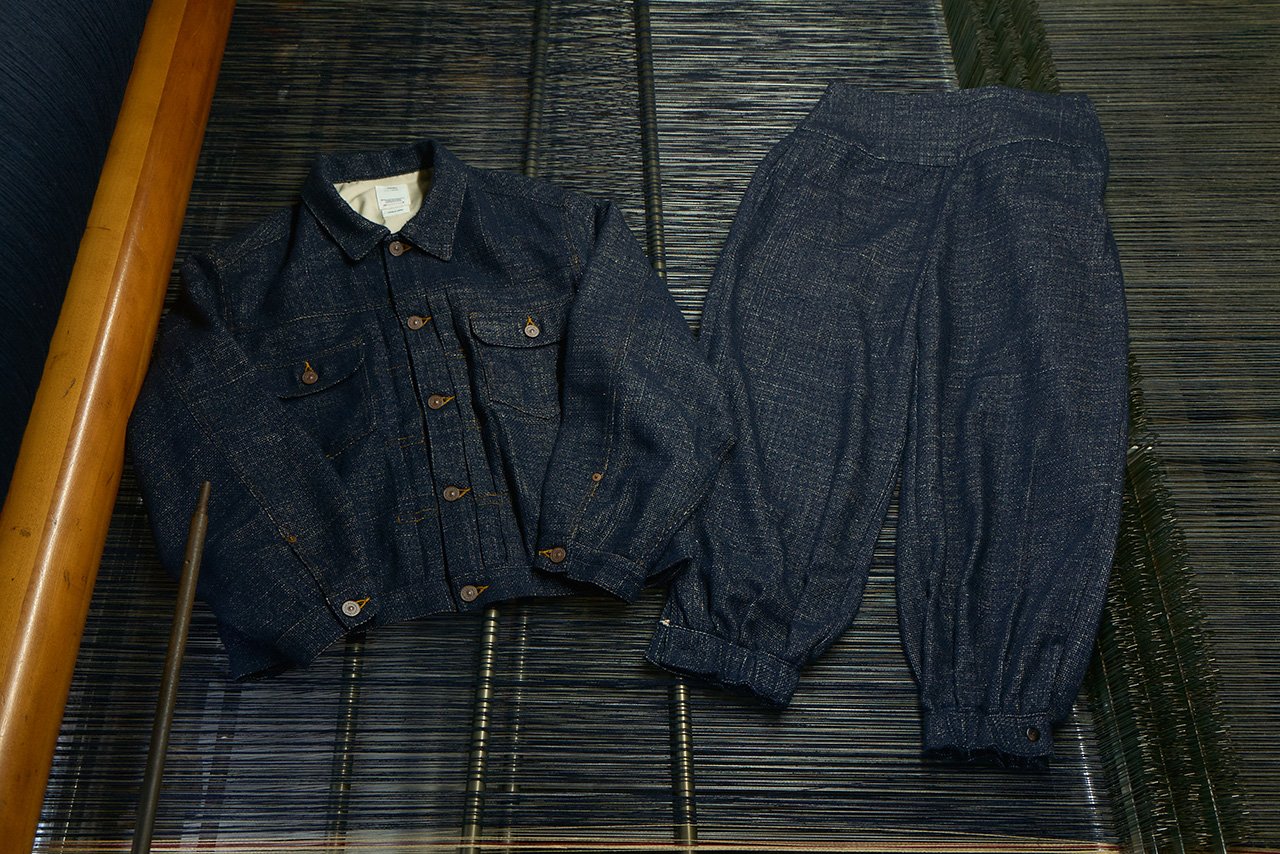
"As we are able to prepare a great variety of looms that can handle different yarn counts, we can create very experimental fabrics in small batches that are not possible in mass production; this is our strength. There are an infinite number of combinations when it comes to materials and techniques, thus we challenge ourselves regularly to try and create new fabrics every day. For a business, it is probably more efficient and easier to mass produce the same thing all the time, however as a maker it's much more enjoyable to answer the needs of our partners that will ask, 'would it be possible to do this?'."
The catalyst for their efforts was rooted in a situation that Japan's textile industry finds themselves in as much of the production has moved overseas where labor costs are lower.
"When I was a child there were over 2,000 weaving shops in the Tango area, but today there are only about 500. If things continue like this, there may only be a few shops left in 10 years. The people that produce are also aging. When we thought about the future, we realized that we couldn't just keep competing to offer a lower price, and we actually needed to create our own unique proposition of value, so we started making new fabrics. We also started making appearances at exhibitions in Tokyo and overseas where over the last 15 years or so we have been able to gradually build a reputation for our work."
The eldest son, Shota, who will turn 23 this year has joined the workshop and has started his training to master the dyeing and warping processes.
"I recently had him join me for a showing at an exhibition in Paris. I believe we have to inform those like him who will succeed us as the next generation that, 'this work can be very satisfying,'."
Text: Kosuke Ide
Photo: Keisuke Fukamizu